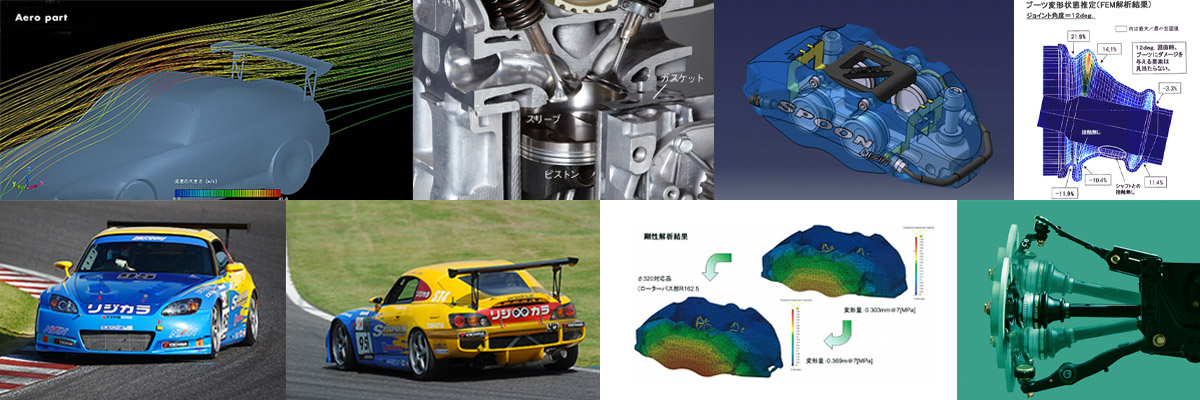
Aero parts proven on the circuit.
Creating down force while reducing drag. These repulsive factors must be balanced at an optimum to produce a truly effective aero part. At Spoon, we combine our knowledge accumulated from all of our years of racing and state-of-the-art CFD (Computational Fluid Dynamics) to develop each of our aero parts for Honda vehicles. All proto-type products are tested on the track and validated from multiple perspectives. To achieve the highest cornering performance. Stability under any circumstance. Only the blatantly honest policy to develop an aero part with surpassing performance leads to the highest quality product.
The quintessential performance is in the braking.
In sports driving, it's really all about the braking. Pressing down on the brake pedal, the nose dives and the driver fights the rear with steering and gas pedal control. Our caliper development focuses on that very moment of excitement. We start from designing the cast. Applying precision aluminum forging technology, the caliper is designed with a 4-piece opposed monocoque structure with variable diameter pistons. The forged caliper support is deeply inserted to the caliper body to securely embrace the hub knuckle. Such design enhances the overall rigidity, minimizing drag torque and bias-wear of brake pads. As the next corner opens its jaws, the driver can fully commit to the last braking point, making the rear follow his lead. Only after mastering the art of braking, the true sensation of sports driving will be rewarded to the driver. Commitment to the true essence of driving. That is where all begins with Spoon.
Polishing, Spoon Standard.
To reach the level of high quality driving experience we strive for, a drive shaft that was both “smooth” and “tough” was essential. Spoon’s drive shaft has an exponentially higher rotation accuracy compared to stock. Every component is polished to mirror-finish to provide lubrication efficiency, resulting in slip-free low vibration. This also prevents metal burn-in or seizure, thus providing higher durability. Our drive shaft significantly reduces noise vibration from the drive train, offering an extremely smooth driving feel. Even the drive shaft boots has been re-developed from material selection and manufactured with custom designed molds. Attention to detail, even to the components and parts our users will never see. The latest technology and craftsmanship backed with creativity and experience are applied to our products. That is Spoon’s philosophy in product development.
A 56mm butterfly?
From the 80’s, Spoon had been increasing the throttle diameter of the throttle body in our racing cars. In the 90’s, Honda started to install such big throttle body to their performance focused engines for increased power and response. Even before Honda began to install big throttle bodies to their production cars, Spoon was applying the technology. To increase the absolute intake air flow, we enlarged the diameter of the throttle butterfly to its limit, the inner wall of the body was grinded and mirror-polished for low resistance, and the geometry of the throttle body was redesigned to benefit from the Venturi effect. Innovation without being restricted to past experience and knowledge. With trial and error, we strive to lead the world in product development. Continuing our challenge to build a “better car”. That’s what Spoon is all about.
2 gaskets in 1.
The main purpose for the gasket is to maintain airtight condition inside the combustion chamber while withstanding extreme temperature and pressure. Honda engines are known to run at high rpms, At above 9000rpms, the cylinder walls of the open-deck structure begins to micro vibrate. The inner wall of the cylinder is steel, wrapped around by aluminum. The rates of thermal expansion between the two materials are different. That creates a height difference at the top of the cylinder. Gaskets blow from such thermal expansion and micro vibrations. When the gasket blows, it sends explosive pressure to the water line, creating serious damage to the cooling system within the engine.
Spoon’s goal was to develop a new gasket specially designed for high revving Honda engines. We laser welded two sheet materials with a 25 micron difference in thickness. The welding line was designed to be at the center of the 6mm wide cylinder wall. This helped to maintain the same compression from cold to high temperatures. The sheet material we used was exactly the same as Honda’s stock gaskets. Applying YAG laser welding was essential to achieving high sealing performance and durability. At first glance, our gasket looks just like stock. We focus on the slightest change in performance and the unique characteristics of each engine to minimize any risks, even if they are small. Such approach is universal to Spoon’s product development.
Why a simple plate can reinforce the body.
This gusset plate was specifically developed to reinforce the body of the S2000. The stock car is designed to be driven on stock tires within sensible speed range. However, we found that the bond between the body and the upper arm of the S2000 was just too vulnerable. We developed this gusset plate to reach the ideal body strength for the S2000.
Even if the problem is a basic design or structural issue of a car, we will release a product to solve it. That is Spoon.